Großes Netzwerk + Smarte Auswahl + Aus einer Hand = Online-Fertigung
Als Online-Fertiger mit einem Netzwerk von mehr als 2000 Fertigungspartnern hat FACTUREE Zugriff auf nahezu unbegrenzte Kapazitäten zur Fertigung von Sonderteilen aller Art und sichert auf diese Weise Ihre Lieferketten.
Unter dem Einsatz von Machine-Learning-Algorithmen finden wir für jedes einzelne Ihrer Projekte – von Prototyp bis Serienfertigung – den optimalen Fertiger in Bezug auf Qualität, Preis und Lieferzeit.
FACTUREE ist während der gesamten Projektabwicklung alleiniger Vertrags- und Ansprechpartner und übernimmt volle Verantwortung für Liefertreue und Qualität der Teile.
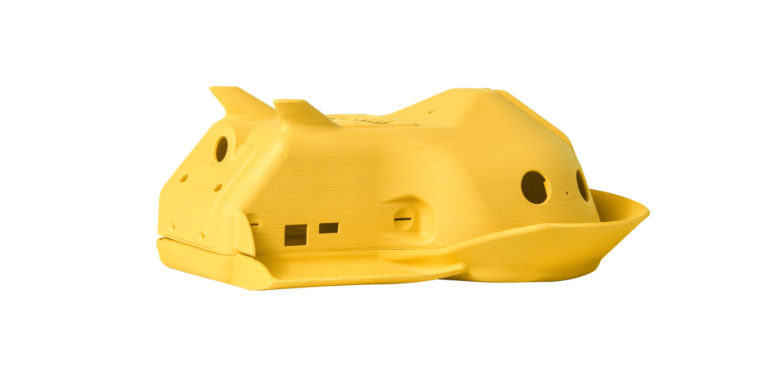
Referenzen
Von Industrie bis internationaler Spitzenforschung
– mehr als 30.000 zufriedene Kunden
Kurze Lieferzeit bei
komplexer Herstellung
Trotz der komplexen Herstellung bei hoher Stückzahl und eng gesetzter Lieferfrist konnte FACTUREE bereits vor dem vereinbarten Liefertermin die Bauteile ausliefern. Weitere Vorteile ergaben sich in der zügigen Auftragsbearbeitung und der persönlichen Kundenbetreuung. Kosten um 15% geringer
als bei anderen Anbietern
Das Angebot von FACTUREE erfolgte schnell und ebenso die Auslieferung der Bauteile. Die Eingangskontrolle war einwandfrei. Die Kosten für die Komponenten waren im Vergleich zu anderen Anbietern in Europa um 15% geringer. Neue Freiheitsgrade durch
stabile Beschaffungsprozesse
FACTUREE entlastet uns bei der Fertigung komplexer Bauteile für spezielle Einsatzbereiche und eröffnet uns dadurch neue Freiheitsgrade. Durch die stabilen Beschaffungsprozesse ist unsere Handlungsfähigkeit jederzeit sichergestellt. 
Einfach zu bedienendes
Beschaffungs-Interface
Wir schätzen FACTUREE als zuverlässigen Lieferanten für Fertigungsteile mit guten Lieferzeiten und einfach zu bedienendem Beschaffungs-Interface. Gerade in Corona-Zeiten bietet diese Art der Beschaffung eine entsprechende Sicherheit. 
Breite Leistungsspektrum und
gute Preisgestaltung
Die Angebotserstellung durch FACTUREE erfolgte sehr schnell, innerhalb von ein bis zwei Tagen. Uns haben sowohl das breite Leistungsspektrum als auch die gute Preisgestaltung sowie die kurzen Lieferzeiten überzeugt. FACTUREE hat bisher alle Liefertermine zu 100 Prozent eingehalten.

3D-Druck
Leistungsangebot:
- alle gängigen Druckverfahren
- Kunststoffe, Resine, Metalle etc.
- inkl. Oberflächenfinishes
- Prototyping und Serienfertigung
Spezifikationen für 3D-gedruckte Teile:
- min. Dimensionen: L: 3mm x B: 3mm x H: 3mm
- max. Dimensionen: L: 1000mm x B: 1000mm x H: 1000mm
- Wandstärke: ab 0,2mm
- Stückzahl: bereits ab 1 Stk.
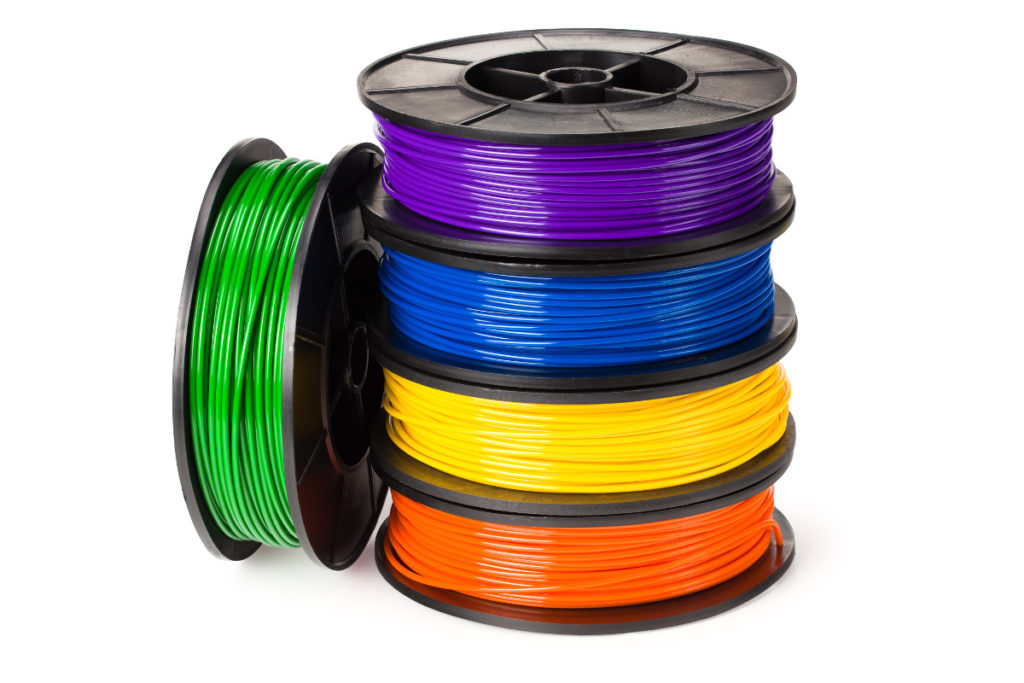
Was ist 3D-Druck?
3D-Druck bezeichnet grundlegend ein Verfahren, bei dem ein Werkstück oder eine komplette Baugruppe Schicht für Schicht aus einem Ursprungsmaterial aufgebaut wird. Aus diesem Prozess ergibt sich auch die Bezeichnung „additive Fertigung“ für den 3D-Druck. Aktuell erlebt der 3D-Druck einen regelrechten Boom, auch und vor allem in der industriellen Fertigung. 2018 wurden weltweit bereits mehr als 18 Milliarden Dollar auf dem 3D-Markt umgesetzt – Tendenz stark steigend. In der Fertigung ist der 3D-Druck mittlerweile zu einer ernstzunehmenden Alternative zu subtraktiven Technologien, beispielsweise Drehen oder Fräsen, geworden.
Auch wenn das Grundkonzept beim 3D-Druck immer gleich ist, so zeigen sich doch signifikante Unterschiede zwischen den einzelnen Verfahren. Neben der Extrusion von Materialien wird auch das Aushärten flüssiger Polymere oder ein selektives Binden von Materialpulver im Bereich des 3D-Drucks eingesetzt.
Additive Fertigungsverfahren
Durch ein großes Netzwerk an Fertigungspartnern ist FACTUREE in der Lage, das gesamte Spektrum der additiven Fertigung abzudecken. Zusätzlich können Sie auch Teile mittels CNC-Fräsen, CNC-Drehen sowie Blechbearbeitung fertigen lassen.
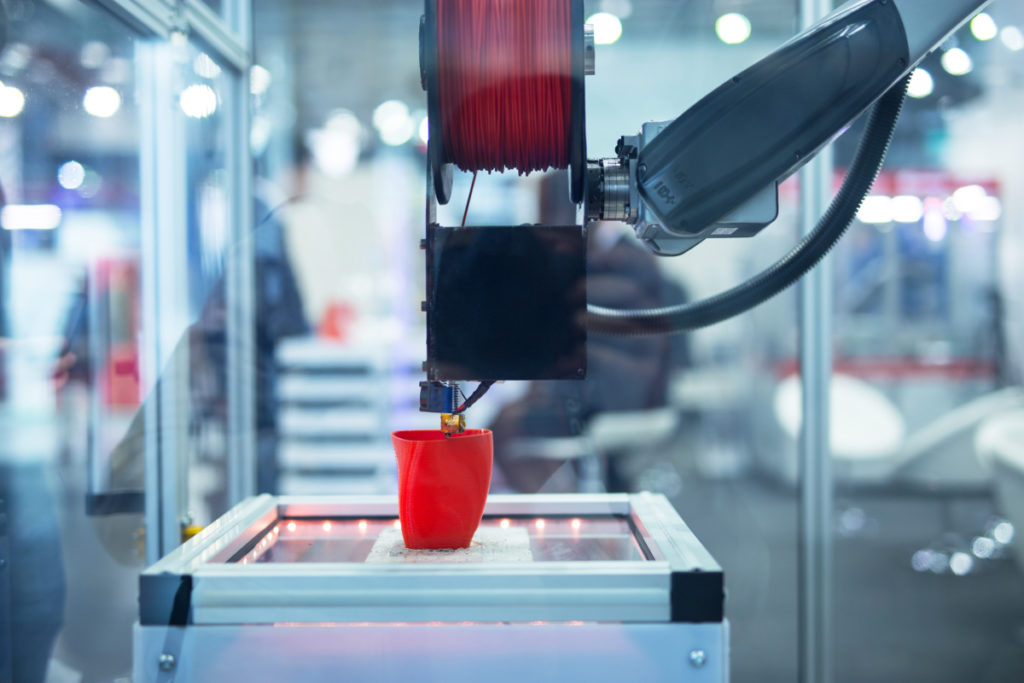
Fused Deposition Modeling ist ein 3D-Druckverfahren, bei dem geschmolzener Kunststoff, in seltenen Fällen auch verflüssigte Metalle, schichtweise auf eine Werkplattform aufgetragen wird. Schicht für Schicht wird so beim FDM ein 3D-Druckmodell erzeugt. Grundlage für das FDM Verfahren ist ein digitales 3D-Modell, welches von speziellen CAD Programmen in eine große Anzahl an einzelnen Schichten (Slices) zerlegt wird. Diese Schichten werden anschließend durch den 3D-Drucker auf die Arbeitsplattform übertragen.
Die Vorteile des Fused Deposition Modelings liegen vor allem in der kostengünstigen, schnellen Durchführung des 3D-Drucks. Hierdurch sind kurze Lieferzeiten und wirtschaftliche Drucke möglich. Die gedruckten Bauteile sind darüber hinaus überaus formstabil. Nachteilig gestalten sich die geringe Genauigkeit der gedruckten Teile und die Sichtbarkeit der einzelnen Druckschichten. Bei bestimmten Materialien, vor allem ABS, können sich dünne Teile verbiegen – der sogenannte „Warp-Effekt“. Ebenfalls in einigen Fällen als nachteilig angesehen werden kann die technische Eigenheit des FDM Drucks, dass Volumenkörper nicht solide, sondern immer mit einer Füllstruktur gedruckt werden.
Als Materialien für den FDM Druck kommen grundsätzlich alle Thermoplaste in Frage. Häufig verwendet werden ABS, Polyamide, PEEK oder PA6. Auch Polycarbonate, PET oder Polypropylene werden für den FDM Druck eingesetzt. Noch in der Erprobung sind FDM Drucke aus Metallen. Dies wird allerdings bis dato noch nicht im industriellen Maßstab umgesetzt.
Die Stereolithographie ist das bis dato am längsten verwendete 3D-Druckverfahren. Bereits 1983 wurde die Stereolithographie (SLA) erfunden – und wird nach wie vor in fast unveränderter Form industriell eingesetzt. Bei der Stereolithographie werden lichtaushärtende Eigenschaften von Photopolymeren genutzt, um Bauteile in 3D zu drucken. Die Photopolymere, beispielsweise Epoxid- oder Kunstharze, befinden sich in einem flüssigen Kunststoffbad. Dieses besteht aus den Basismonomeren des Kunststoffes. Ein Laser dient dazu, die Kunststoffe an den durch ein CAD-Modell vorgegebenen Stellen auszuhärten. Ist eine Schicht ausgehärtet, senkt sich die Arbeitsplattform des 3D-Druckers einige Millimeter ab. Ein Wischer verteilt eine neue Schicht flüssigen Kunststoffs und der Laser kommt erneut zum Einsatz. Schicht für Schicht wird so das gewünschte Objekt aufgebaut.
Als Material für die Stereolithografie kommen technisch bedingt ausschließlich photosensitive Kunststoffharze (Epoxid, Acylat oder Elastomer) zum Einsatz. SLA dient der Anfertigung filigraner Modelle, Designmodelle und Prototypen, aber auch zur Herstellung von Funktionsbauteilen oder Urmodellen zum Abformen. Als Nachteil muss die Sprödigkeit der erstellten Objekte erwähnt werden, die die Anwendungsgebiete einschränkt. Da umfangreiche Nacharbeiten wie das Aushärten der Objekte in einem UV-Schrank oder das manuelle Entfernen von Stützstrukturen beim SLA Druck nicht zu vermeiden sind, ist das Verfahren vergleichsweise kostenintensiv.
Feste Bauteile mit hoher Genauigkeit, hoher Auflösung und das in kürzester Zeit: Multi Jet Fusion ist zweifelsohne eine der derzeit leistungsfähigsten Technologien im Bereich des 3D-Drucks. Bei dem Verfahren wird eine wärmeleitende Flüssigkeit, der sogenannte „Fusing Agent“ auf eine Schicht des Materialpulvers (in der Regel Polyamid 12) aufgetragen. Direkt im Anschluss wird eine Infrarot-Wärmequelle eingesetzt. Der Fusing Agent sorgt dafür, dass die durch ihn benetzten Bereich stärker erhitzt werden als das restliche Materialpulver. Dies sorgt für ein Zusammenschmelzen des Materials. Um scharfe Kanten und genaue Konturen zu realisieren, kommt ein weiterer Wirkstoff, der „Detailing Agent“ zum Einsatz. Dieser Agent wird exakt um die Bereiche herum aufgetragen, auf welchen der Fusing Agent verwendet wird. So entsteht ein deutlicher Temperaturunterschied – und es entstehen die gewünschten, scharfen Kanten und genauen Konturen.
Die Vorteile des Multi Jet Fusion Verfahrens liegen in der fast 100-prozentigen Dichte der gedruckten Bauteile und der hohen Geschwindigkeit des Drucks. Die Druckgeschwindigkeit bei MJF liegt rund 10mal höher als bei anderen, vergleichbaren Verfahren. Durch die kleinen Tropfen, die beim Multi Jet Fusion für den 3D-Druck verwendet werden, übersteigt die Auflösung (1.200 dpi) jede andere additive Fertigungsmethode. Als nachteilig lässt sich die etwas raue Oberfläche der gedruckten Objekte und die Beschränkung auf nur ein Material aufführen (PA 12). Wenn andere Farben als Grau oder Schwarz für die gedruckten Objekte erwünscht sind, fallen extra Kosten für eine Beschichtung an.
Das PolyJet Verfahren, stellenweise auch MultiJet Modeling genannt, ist eines der am weitesten verbreiteten Verfahren im Rapid Prototyping. Für den 3D-Druck wird beim PolyJet Verfahren mittels eines Druckkopfs ein in winzige Tröpfchen verteiltes Photopolymer in Schichtbauweise auf eine Bauplattform aufgetragen und dort umgehend durch UV-Licht ausgehärtet. Im PolyJet 3D-Druck sind feinste Schichtdicken von nur 16 – 32 µm möglich, was den Modellen eine extrem hohe Detailgenauigkeit verleiht. Weiterhin entstehen glatte Oberflächen, die denen aus dem Spritzguss nahekommen. Auch ist es problemlos möglich, beim PolyJet Druck mehrere unterschiedliche Materialien für ein Werkstück zu kombinieren. So lassen sich beispielsweise feste und gummiartige Materialien kombinieren oder unterschiedliche Materialien schon während des 3D-Drucks vermengen, so dass komplett neue Werkstückeigenschaften entstehen. Neben diesen Vorteilen muss aber auch erwähnt werden, dass der PolyJet 3D-Druck lange Druckzeiten mit sich bringt, was die Fertigung recht kostenintensiv macht. Auch sind für den Druck stellenweise Stützkonstruktionen erforderlich. Dadurch müssen die gedruckten Werkstücke häufig manuell nachbearbeitet werden, was den Preis zusätzlich in die Höhe treibt.
Beim selektiven Lasersintern (SLS) wird ein pulverförmiges Ausgangsmaterial – zumeist Polyamid oder Elastomer – vollflächig auf die Werkplattform des 3D-Druckers aufgetragen. Anschließend wird das Pulver gemäß der vorgegebenen Kontur durch einen Laserstrahl gesintert, sprich bis kurz unter den Schmelzpunkt erhitzt. Das Material verbindet sich dadurch entlang der gewünschten Kontur. Ist eine Schicht fertiggestellt, senkt sich die Bauplattform um die Stärke der Schicht ab. Es wird eine neue Pulverschicht aufgebracht und der Vorgang beginnt von neuem. Schicht für Schicht und von unten nach oben entsteht so das gewünschte Objekt im 3D-Drucker. Da überhängende Strukturen im Pulverbett stabilisiert werden, ist die Anbringung (und anschließende Entfernung) von Stützstrukturen nicht notwendig. Die erstellten Bauteile sind mechanisch belastbar, thermostabil und leicht. Weiterhin lassen sich durch SLS ineinander verzahnte und dadurch bewegliche Objekte drucken. Als nachteilig beim SLS Verfahren können die vergleichsweise raue Oberfläche und die langen Druckzyklen erwähnt werden. Auch sind die erzielbaren Toleranzen höher als bei anderen Verfahren wie der Stereolithographie oder dem PolyJet-Verfahren.
Wie bereits erwähnt wird für SLS hauptsächlich Polyamid als Werkstoff eingesetzt. Seltener kommen auch thermoplastische Polyurethane (TPU) oder Polyether Ketone (PEK) beim selektiven Lasersintern zum Einsatz. Wird PA12 (Nylon) für SLS verwendet, kann dieses mit Ergänzungen angereichert werden, um spezifische Materialeigenschaften zu erzielen. Ergänzungsmaterial ist hier beispielsweise Aluminium oder auch Kohlefaser.
Das selektive Laserschmelzen (SLM) gilt als eines der vielseitigsten 3D-Druckverfahren und als rentable Alternative zum Schweißen, Fräsen oder Gießen. Beim selektiven Laserschmelzen wird Metall in Pulverform auf eine Bauplattform aufgebracht und anschließend mittels Laserstrahl entlang der gewünschten Kontur geschmolzen. Auch beim SLM wird schichtweise gearbeitet, was bedeutet, dass sich die Bauplattform nach Erstellen einer Schicht absenkt, frisches Pulver aufgebracht und anschließend erneut geschmolzen wird. Benötigte Stützstrukturen werden parallel zum eigentlichen Druck automatisch mit eingebaut.
Der Vorteil des SLM liegt eindeutig in der Konstruktionsfreiheit. Da die Bauteile Schicht für Schicht in der gewünschten Form aufgebaut werden, lassen sich selbst extrem komplexe Geometrien und bewegliche Teile aus schwer zerspanbaren Materialien generieren. Durch minimalste Abfallmengen ist das selektive Laserschmelzen gleichzeitig überaus wirtschaftlich. Als Werkstoffe kommen Aluminium, Edelstahl, Titan oder Kobalt-Chrom-Legierungen zum Einsatz. Abhängig vom Hersteller oder Fertigungsbetrieb wird selektives Laserschmelzen auch als DMLS (Direct Metal Laser Sintering), LMF (Laser Metal Fusion) oder Additiv Layer Manufacturing bezeichnet. Die unterschiedlichen Begriffe bezeichnen jedoch alle das gleiche Verfahren.
Neben den in der Industrie gängigen Verfahren existieren weitere 3D-Druck Möglichkeiten. So zum Beispiel das 3D Printing, bei dem gipsartiges Pulver schichtweise mittels eines Bindemittels verklebt wird. Oder das Digital Light Processing (DLP), welches im Groben der Stereolithographie ähnelt. Allerdings wird hier für das Aushärten des Grundmaterials ein Projektor oder ein LCD Display anstelle eines Lasers eingesetzt. Auch das Elektronenstrahlschmelzen (EBM) wird stellenweise für den 3D-Druck eingesetzt. EBM erfordert immer ein leitfähiges Material in Pulverform. Das Material wird im 3D-Drucker mit Energie aus Elektronen „beschossen“ und somit zum Schmelzen gebracht.
Welches 3D-Druckverfahren letztendlich das wirtschaftlichste, schnellste und für den jeweiligen Anwendungszweck optimale ist, lässt sich nicht allgemeingültig beantworten. Jedes Verfahren hat seine ganz eigenen, spezifischen Vor- und Nachteile. Daher ist für jeden 3D-Druck abzuwägen, welches Verfahren als geeignet ausgewählt werden soll.
Materialauswahl für 3D-Druck
Profitieren Sie von unserem Netzwerk mit der größten Materialauswahl am Markt. Kaum ein Material, das für Ihre 3D-Druckteile nicht kurzfristig beschafft werden kann. Falls es doch einmal vorkommt, finden wir nahezu immer eine geeignete Alternative.
- ABS
- PC
- PEEK
- PEI
- PET
- PETG
- PLA
- Polyamid (Nylon)
- PP
- Silikone
- u.v.m.
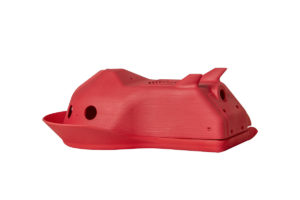
- Standard
- Clear
- Durable
- Flexible
- High Temp
- PC-ähnlich
- u.v.m.
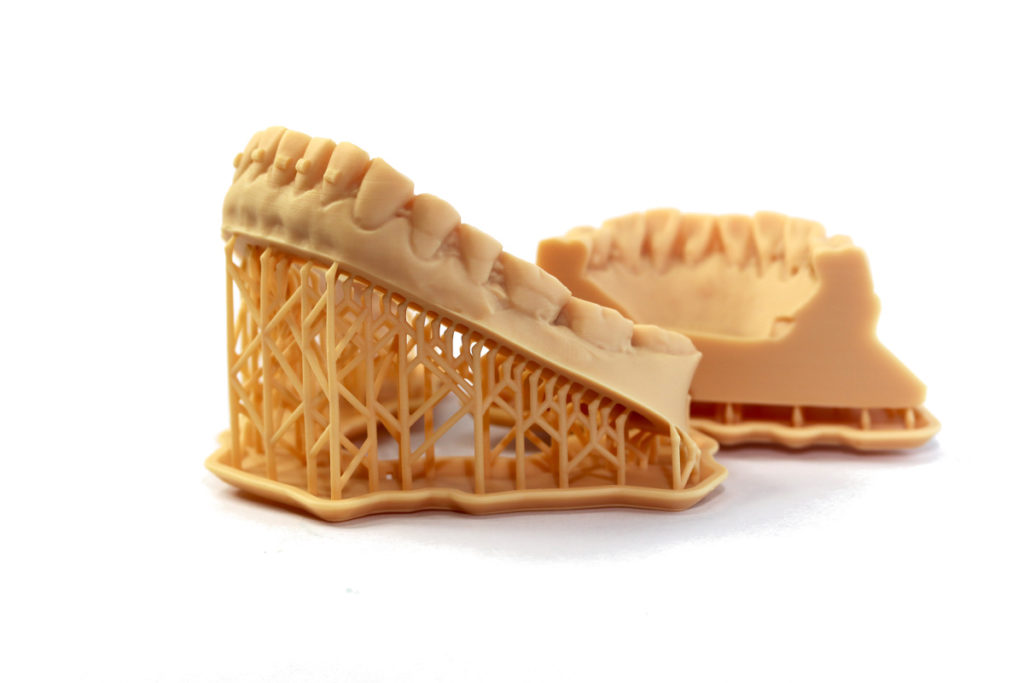
- Aluminium
- Edelstahl
- Inconel
- Titan
- u.v.m.
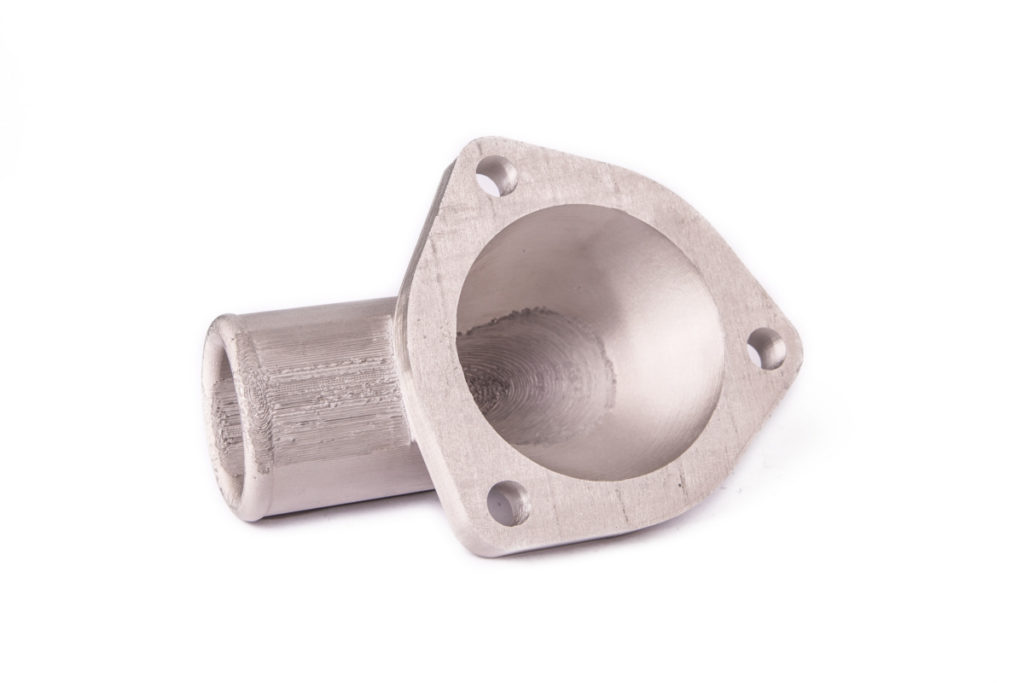
- Verbundstoffe z.B. Alumide
- Polymergips
- weitere Materialien auf Anfrage
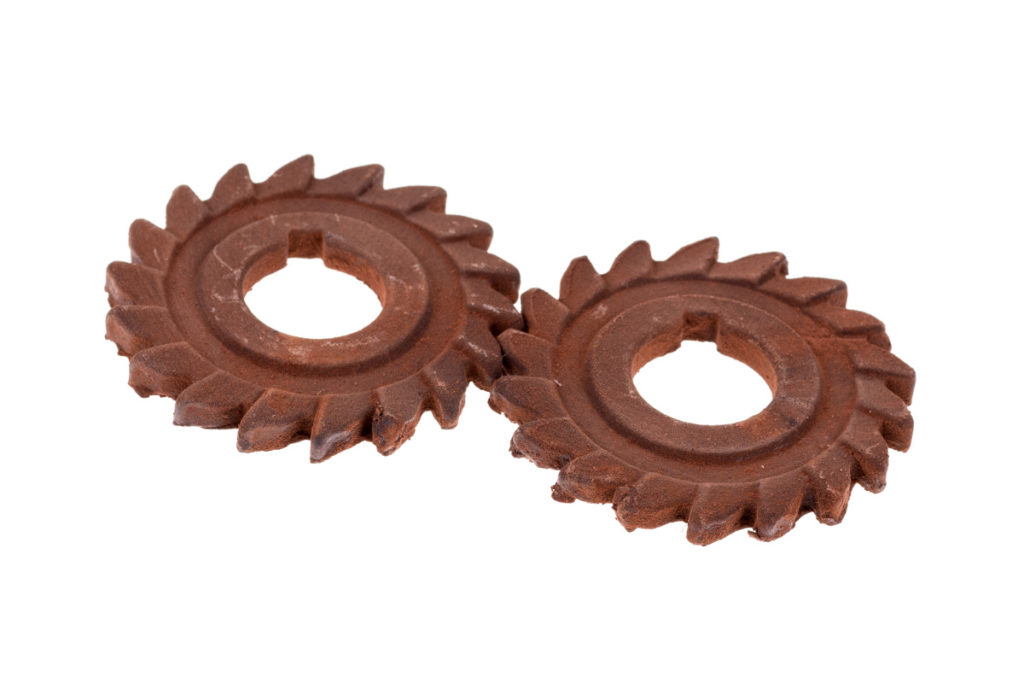
3D-Druck – mehr als Prototyping
Bei FACTUREE erhalten Sie 3D-Druckteile in allen Stückzahlen, vom einzelnen Prototypen bis zur Massenproduktion. Lassen Sie Ihr Angebot individuell auf Preis oder Lieferzeit optimieren. Wir beraten Sie gerne.
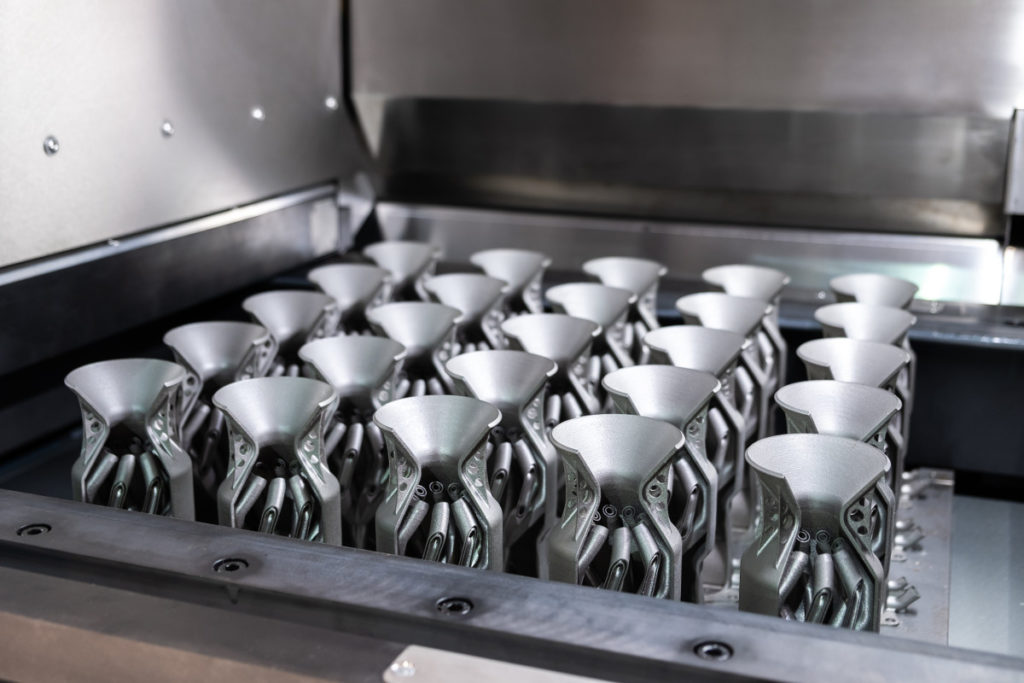
Beim Prototyping zählt oftmals jeder Tag. Online-Fertigung ist mittlerweile zu einem Synonym für Geschwindigkeit geworden. Durch unser großes Netzwerk an Fertigern haben wir stets freie Kapazitäten und kurze Lieferzeiten.
Auch die Beschaffung von Serienteilen per Online-Fertigung ist vorteilhaft. Durch die smarte Auswahl eines hochspezialisierten Fertigers kann in hoher Stückzahl kosteneffizient produziert werden. Lassen Sie uns kostenlos prüfen, ob wir Ihre aktuellen Einkaufspreise unterbieten können.
Rahmenverträge bieten Unternehmen langfristige Preisstabilität und damit Planungssicherheit. Rahmenverträge können mit FACTUREE individuell gestaltet und auf Ihre Bedürfnisse zugeschnitten werden.
Case Study: Festo
Festo baut bei Entwicklung von Funktionsprototypen auf Zulieferteile von Online-Fertiger FACTUREE
Online-Fertiger liefert gespante Einzelteile für Prototypen – Zeit- und Kosteneinsparungen als zentrale Vorteile

In der Fabrik- und Prozessautomatisierung spielt pneumatische und elektrische Steuerungs- und Antriebstechnik eine bedeutende Rolle. Festo, weltweit führender Hersteller von Automatisierungstechnik, bedient den Markt mit entsprechenden Produkten, Systemen und Services für unterschiedlichste Anforderungen. Um bereits in der Entwicklung neuer Serien effizient zu agieren, setzt Festo auf den Online-Fertiger FACTUREE als Lieferant von gespanten Einzelteilen für Funktionsprototypen. Die Vorteile: FACTUREE bietet ein breites Fertigungsspektrum, schnelle Bereitstellungszeiten sowie fristgerechten Lieferungen. Festo wird damit unterstützt, sich stets flexibel und qualitativ hochwertig auf die aktuellen Kunden- und Marktanforderungen einzustellen.
Die Festo SE & Co. KG mit Stammsitz in Esslingen am Neckar ist eine auf Steuerungs- und Automatisierungstechnik spezialisierte Unternehmensgruppe. Das unabhängige Familienunternehmen agiert als Global Player und beliefert 300.000 Kunden in über 35 Branchen mit pneumatischer und elektrischer Automatisierungstechnik. Festo verfügt über die Geschäftsbereiche Automation (Automatisierungstechnik) und Didactic (Lernsysteme, Training und Consulting). Das Unternehmen ist weltweit führend in der Automatisierungstechnik und Weltmarktführer in der technischen Aus- und Weiterbildung.
Kurzfristige Bereitstellung von Bauteilen für Funktionsprototypen erforderlich
Festo bringt regelmäßig Neuentwicklungen auf den Markt. Diese Produktneuheiten werden Voruntersuchungen bzw. umfangreichen Funktionsprüfungen unterzogen. Dazu werden immer wieder neue Bauteile benötigt, deren Bereitstellung in kurzer Zeit erfolgen werden muss. Um Entwicklungsprozesse nicht zu verzögern und gleichzeitig eigene Ressourcen zu schonen, lässt Festo gespante Einzelteile von „FACTUREE – Der Online-Fertiger“ zuliefern.
Bodo Neef, Entwicklungsingenieur bei Festo, erklärt: „Bisher gab es oft zeitliche Engpässe in der Beschaffung von Prototypenteilen. Wir sind aus diesem Grund dazu übergegangen, die Fertigung der entsprechend benötigten spanend hergestellten Teile dem Online-Fertiger zu übergeben.“
Bei FACTUREE handelt es sich um eine Marke der cwmk GmbH, die über ein umfangreiches Produktionsnetzwerk verfügt, dem aktuell mehr als 500 Fertigungspartner aus den Bereichen CNC-Bearbeitung und Oberflächentechnik mit ca. 6000 Maschinen angehören. Alle Partner unterliegen einem kontinuierlichen datengetriebenen Qualitätsmanagementsystem, das nach ISO 9001 zertifiziert ist. Die Vorteile liegen in dem breiten Spektrum an Netzwerkpartnern, Fertigungstechniken und Oberflächenbehandlungen. So können Einsparpotenziale, Effizienzgewinne und eine erhöhte Liefertreue erzielt werden, da stets freie Kapazitäten und kurze Lieferzeiten garantiert sind.
So betraute Festo das Berliner Unternehmen FACTUREE unter anderem mit der Fertigung von gespanten Einzelteilen für die Voruntersuchung eines neuen Stellungsreglers. Dazu wurden unter anderem Ventilblöcke unterschiedlicher Bauart benötigt. Der Auftrag beinhaltete die vollständige mechanische Bearbeitung spezieller Einzelteile.
Axel Müller, Entwicklungsabteilung Stellungsregler bei Festo, sagt: „Die benötigten Bauteile besitzen ihren Anspruch in den sehr komplexen Konturen und der hohen Oberflächenqualität. FACTUREE passte von allen evaluierten Anbietern am besten zu unserem Anforderungsprofil. Die vielfältigen Fertigungsarten und -möglichkeiten sowie die zugesicherte schnelle Lieferzeit und unkomplizierte Angebotserstellung waren entscheidende Kriterien. Es gibt einige Anbieter, die ein ähnliches Portfolio anbieten, aber sie konnten nicht in der Kürze der Zeit liefern.“
Einfacher und schneller Beschaffungsprozess durch Online-Fertigung
Der Beschaffungsprozess gestaltete sich dabei denkbar einfach: Im Hause Festo erstellte 3D- und 2D-Daten dienten FACTUREE als Fertigungsvorlage. Die Angebotserstellung erfolgte schnell. Auf der Website von FACTUREE konnte Festo die vorbereiteten Daten per Upload übermitteln und anschließend die gewünschte Fertigungsart sowie das Material auswählen.
Bodo Neef erklärt: „Die Auslieferung der Bauteile war fristgerecht. Eine Bauart der in Auftrag gegebenen Ventilblöcke erwies sich in der Funktionsüberprüfung als einwandfrei und konnte sofort eingesetzt werden. Das andere Bauartmuster wurde an FACTUREE zur Nacharbeit zurückgesandt, da es einen kleinen Fehler enthielt. Der Support gestaltete sich durchgehend sehr positiv. Die nachzubearbeitenden Teile wurden umgehend von einem von FACTUREE beauftragten Transportdienstleister abgeholt und nach der zügigen Überarbeitung erneut an uns ausgeliefert.“
Die von FACTUREE gelieferten Bauteile erfüllten sämtliche Vorgaben und gewünschte Eigenschaften.
Zusammenarbeit auch in der Zukunft geplant
Festo ist ein langjähriger Kunde von FACTUREE und beabsichtigt, die Zusammenarbeit mit dem Bauteilelieferanten auch in Zukunft weiter zu betreiben und an künftige Anforderungen anzupassen.
„FACTUREE entlastet uns bei der Fertigung komplexer Bauteile für spezielle Einsatzbereiche und eröffnet uns dadurch neue Freiheitsgrade. Durch die stabilen Beschaffungsprozesse ist unsere Handlungsfähigkeit jederzeit sichergestellt. Mit den zahlreichen Fertigungspartnern im Produktionsnetzwerk kann uns FACTUREE stets freie Kapazitäten bieten. Auch die sehr moderate Preiskalkulation haben wir als positiven Aspekt verbucht“, resümiert Axel Müller.
Zahlreiche Vorteile gegenüber konventioneller Beschaffung von 3D-Druckteilen
Schnell
- Konstant kurze Lieferzeiten
- Angebot meist noch am selben Tag
- Einfache Online-Anfrage
- Europaweiter Express-Versand
Universell
- Breitestes Fertigungsspektrum am Markt
- Prototyping, Klein- und Großserien
- 300+ Materialien konstant verfügbar
- Alles aus einer Hand
Verlässlich
- Unbegrenzte Produktionskapazitäten
- Niedrige Reklamationsrate
- ISO 9001-zertifiziertes Qualitätsmanagement Download
- Persönlicher Kundenbetreuer
Whitepaper Mediathek
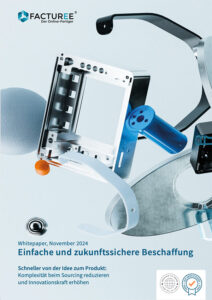
Einfache und zukunftssichere Beschaffung
FACTUREE hat in einer umfassenden Marktforschungsstudie die größten Herausforderungen und Bedürfnisse in der Beschaffung analysiert. Dieses Whitepaper liefert exklusive Studienergebnisse und zeigt, wie Unternehmen Komplexität im Sourcing reduzieren, Prozesse optimieren und ihre Beschaffung zukunftssicher aufstellen können.
November 2024
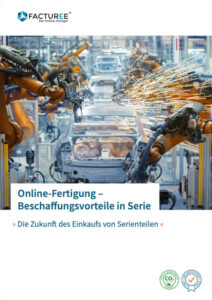
In Serie produzierende Unternehmen befinden sich in einer nie dagewesenen Situation, was die Beschaffung anbetrifft. Unsicherheiten und Krisen schaffen erschwerte Bedingungen und machen selbst kurzfristige Planbarkeit oftmals unmöglich. Gleichzeitig gilt es, sich im Zuge der Digitalisierung neu auszurichten und auf sich ständig verändernde Wettbewerbssituationen zu reagieren.
16 Seiten
Online-Fertigung – Beschaffungsvorteile in Serie
Februar 2023